We’ve written extensively about the topic of workplace safety, covering federal safety posting requirements, the process the Occupational Safety and Health Administration (OSHA) uses to conduct worksite inspections, and what a successful safety program looks like. What we haven’t really touched on, however, is why employers should make safety such an integral part of both their day-to-day operations as well as their overall company culture.
As an employer, you don’t just have an ethical obligation to provide a safe working environment for your employees - you have a legal obligation as well. The Occupational Safety and Health (OSH) Act of 1970 established that employers have certain responsibilities when it comes to their workers’ safety, including providing a safe working environment free from serious recognized hazards. Companies who are found to be out of compliance with OSHA’s established health and safety standards can find themselves facing significant fines or even lawsuits.
A true culture of safety, however, focuses less on these obligations and more on the tangible and intangible benefits a commitment to workplace safety can provide: lower costs associated with work-related injuries and illnesses, increased worker productivity and higher overall levels of employee engagement.
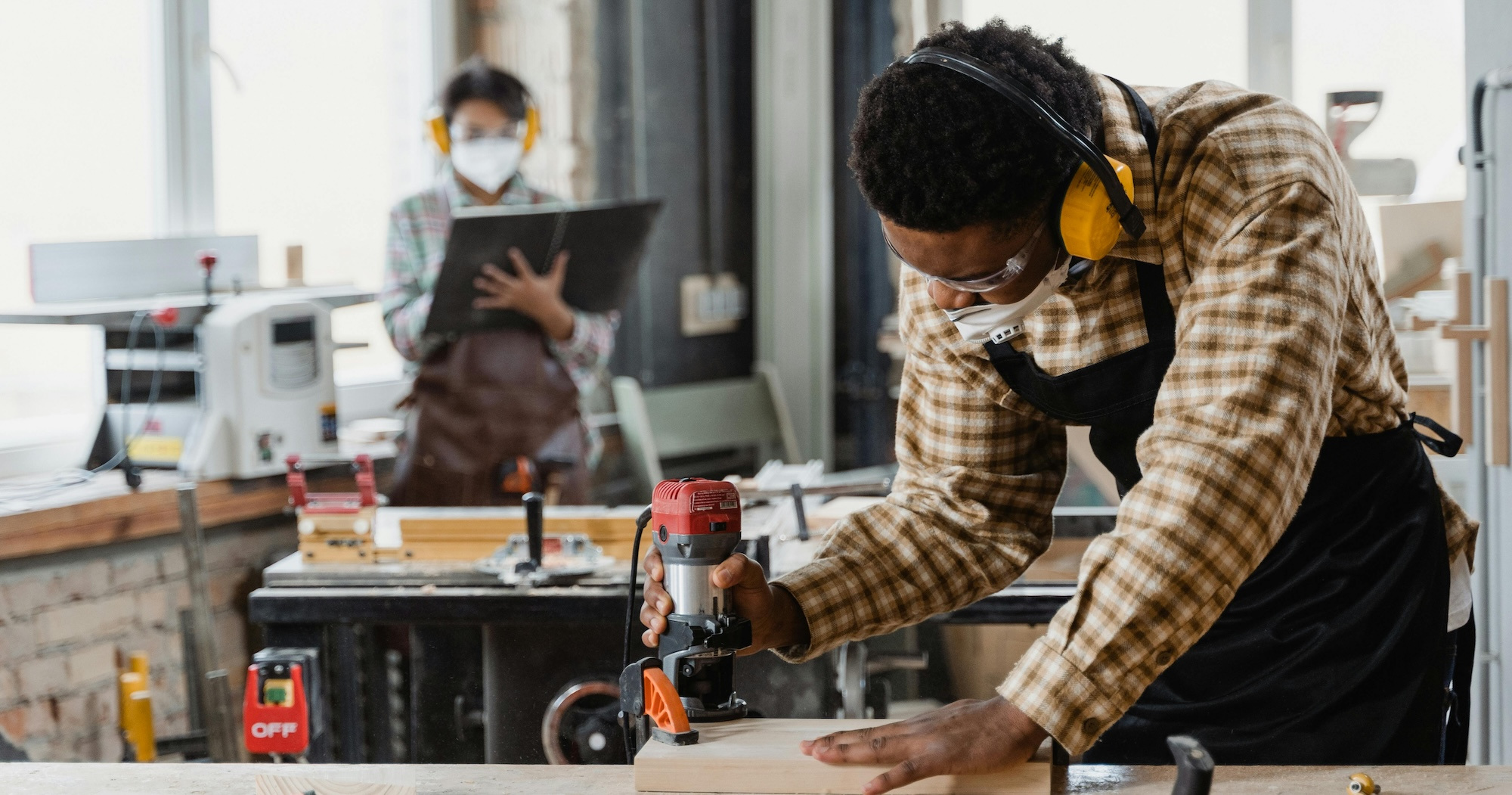
Safety Culture vs. Safety Program
If your organization has a formal safety program in place, congratulations. You’re already one step ahead of many of your peers. But having a safety program doesn’t necessarily equate to having a culture of safety.
A safety program consists of established policies and procedures designed to prevent incidents and mitigate risk. While these policies and procedures are certainly necessary, think of them more as building blocks for your safety culture, not your end goal. The same goes for things like personal protective equipment (PPE), regular audits and workplace ergonomics initiatives.
A safety culture is more of an attitude or approach. When an employer makes a conscious effort to integrate safety into every facet of its business model, then, and only then, have they achieved a truly effective safety culture.
Four absolutely essential things employers have to start doing in order to create an effective safety culture:
- Set the standard.
As with any initiative, a commitment to safety has to start at the top of the organization, with every member of the management or leadership recognizing and understanding the value instilling a culture of safety can have on their organization. Once everyone at the top of the organization has bought into the idea, it’s then their job to not only communicate the expected standards to their employees, but also to live by them. - Empower employees.
The ability to take responsibilities for employee safety can’t just stay with a company’s C-suite or management team. In order to truly build an effective safety culture, every employee needs to not only be aware of all the safety policies and procedures, but also be given the authority to stop work if they notice a safety hazard. - Stop playing the blame game.
Pointing fingers solves nothing. Sometimes employees choose not to speak up about possible hazards (like a piece of broken equipment) because they are afraid that they’ll be blamed or penalized for simply reporting a hazard. Shifting the focus from finding someone to blame to proactively addressing hazards will radically change the way your employees think about safety. - Stop basing your success solely on lagging indicators.
Lagging indicators (things like the number of lost workdays in a year, workers’ compensation costs, incident frequency/severity statistics) measure a company’s previous performance. Leading indicators (things like the number of safety trainings conducted, safety assessments, employee perception surveys) measure future performance. Employers that only measure the effectiveness of their safety programs on lagging indicators are doomed to a reactionary approach to workplace safety.
G&A Partners’ workplace safety services include:
- A written employee safety manual;
- Regular safety audits and inspections;
- Full consultation and assistance with OSHA inspections;
- Post-audit safety meetings/trainings;
- Monthly distribution of safety training materials;
- Maintenance of backup safety records and documentation;
- … and more.
How G&A Can Help
At G&A Partners, we believe prevention is the best defense against workplace accidents. Our team of highly trained workplace safety and risk management professionals help our clients design and administer safety programs that not only ensure they remain compliant with federal safety standards, but also provides them with the training, resources and support they need to make sound decisions regarding the health and safety of their employees.
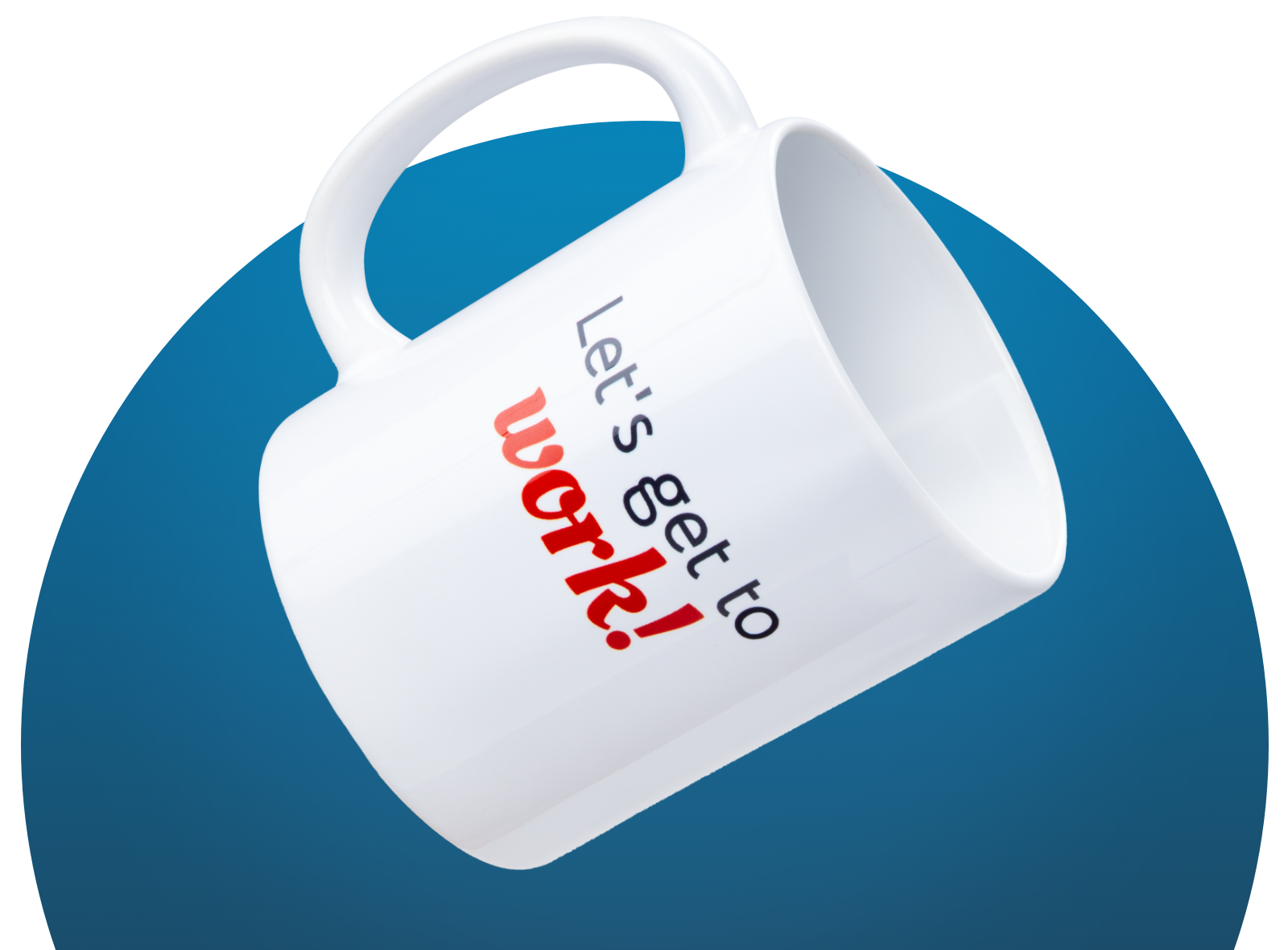