The 4 Approaches Employers Take to Workplace Safety
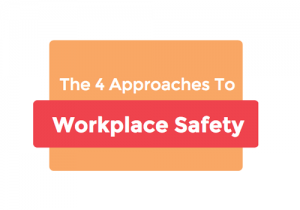
While the safety of each and every employee is a concern common to all organizations, the approaches employers take when it comes to workplace safety vary greatly, particularly from industry to industry. Because the rate of work-related injuries and illnesses tends to be much higher for businesses in what’s referred to as “goods producing” industries (construction, manufacturing, mining, etc.) than those in “service providing” industries (retail, education, professional services, etc.), workplace safety is often a much more top-of-mind concern for these employers.
But no matter what industry your business is in, creating and maintaining a safety-conscious culture is something that should always be near the top of your list of priorities, because the alternative is quite expensive: The national Occupational Safety and Health Administration (OSHA) estimates that employers pay almost $1 billion per week in direct costs related to workplace injuries and illnesses. And employers who are found to have violated OSHA’s federal workplace safety standards can face steep penalties.
Whether you’re just beginning to look into building a safety program, or looking for ways to enhance an existing program, you should be aware that there are four main approaches employers tend to take to workplace safety:
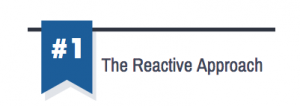
The Reactive Approach
The reactive approach is the one most often taken by employers who are just starting out, as well as smaller, localized companies. Employers who take this approach are often unsure of the various standards they may need to comply with, and may not understand how the laws and agencies that regulate employers may affect them. As such, they are only capable to responding and reacting to an incident after it occurs.
Characteristics of the reactive approach:
- Nonexistent or minimal safety programs.
Companies who use a reactive approach also tend not to have any formal or established safety policies (i.e. written safety manual). - A lack of management buy-in.
Companies who take a reactive approach to safety often do so because managers and executives don’t fully buy-in to the program. With this kind of approach, front-end supervisors don’t always follow what recommended preventative measures or procedures may be in place, causing employees to think they don’t need to follow safety protocols either. - Limited access to funds.
When management doesn’t value a program, they definitely don’t fund it. An effective accident prevention program cannot be built without access to resources.
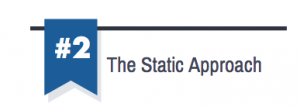
The Static Approach
The static approach is the next step above the reactive approach, and is one that many businesses choose to employ. Companies who use this approach tend to view workplace safety as necessary, but not necessarily a vital part of their business plan.
Characteristics of the static approach:
- Informal safety processes.
Companies who use the static approach make more of an effort to establish some safety processes, but these are largely still informal and used inconsistently. They may discuss safety issues in staff meetings, but usually only to address a recent incident. - Management’s attitude is “pay as you go.”
Employers who fall into this category are focused on managing safety issues as they come up. Similar to the reactive approach, action is taken only after an incident has occurred. While funds are allocated more readily to safety initiatives, this is only done on an “as-needed” basis. - Employees are not empowered to address safety concerns.
If an employee notices a possible hazard, they are not empowered to fix it. Instead, they must report the issue to their direct supervisor, who made in turn need to report it to their supervisor, until the issue reaches the appropriate level of management that has the authority to address the problem. Depending on how high the problem needs to be escalated until it can be addressed, the problem may take weeks or months to be addressed, if it is addressed at all.
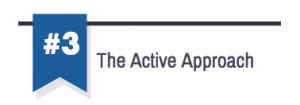
The Active Approach
Employers with some experience in safety issues, such as those with a history of incidents or who have been inspected by OSHA, are usually then motivated to take a more active approach to workplace safety.
Characteristics of the active approach:
- Management is willing to invest funds in order to reduce risk.
Employers in this category understand the role safety and accident prevention processes play in their business’ overall productivity, and will budget money accordingly in order to make necessary safety improvements. In fact, safety improvements are often included as a line item in the business’s operational budget. - Safety processes are documented and enforced.
Employers who use an active approach not only have safety processes and procedures, but are also documented in a safety or employee manual and are actively enforced. - A behavioral safety culture.
In an active approach, employees are not only empowered to address safety concerns, but are expected to address them.
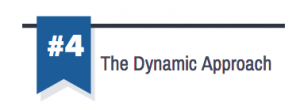
The Dynamic Approach
The final and most effective approach is the dynamic approach. Companies who take this approach are truly invested and committed to creating a culture of safety within their organization.
Characteristics of the dynamic approach:
- Management views safety and accident prevention as a business metric.
Companies that use a dynamic approach understand both their legal responsibilities as an employer to provide a safe working environment, as well as the impact a culture of that is focused on safety can have on their profit margins. Their incidence rates are closely monitored and measured to more effectively control short- and long-term risks. - Safety issues are regularly discussed across all levels.
Employers in this category not only have documented processes and procedures in place, but they also provide workers with regular safety training to ensure that all employees are aware of these processes and how to address possible safety hazards. - Funds are strategically allocated to safety initiatives.
Not only are safety initiatives part of the company’s budget, a great deal of consideration and weight is given to the need for safety improvements.
Conclusion
The ROI of workplace safety programs is undeniable. Employers who make a commitment to creating programs that engage employees across all levels of the organization, conduct regular safety audits, actively work to prevent and control hazards and provide ongoing safety training will see drastic differences, not only when it comes to the number of workplace accidents and injuries and the associated costs, but also in the level of employee morale within their organization.
At G&A Partners, we believe prevention is the best defense against workplace accidents. Our team of highly trained workplace safety and risk management professionals help our clients design and administer safety programs that not only ensure they remain compliant with federal safety standards, but also provides them with the training, resources and support they need to make sound decisions regarding the health and safety of their employees.
G&A Partners’ workplace safety services include:
- A written employee safety manual;
- Regular safety audits and inspections;
- Full consultation and assistance with OSHA inspections;
- Post-audit safety meetings/trainings;
- Monthly distribution of safety training materials;
- Maintenance of backup safety records and documentation;
- … and more.
To learn more about our workplace safety services, call 1-866-634-6713 to speak to an expert, or schedule a free business consultation.